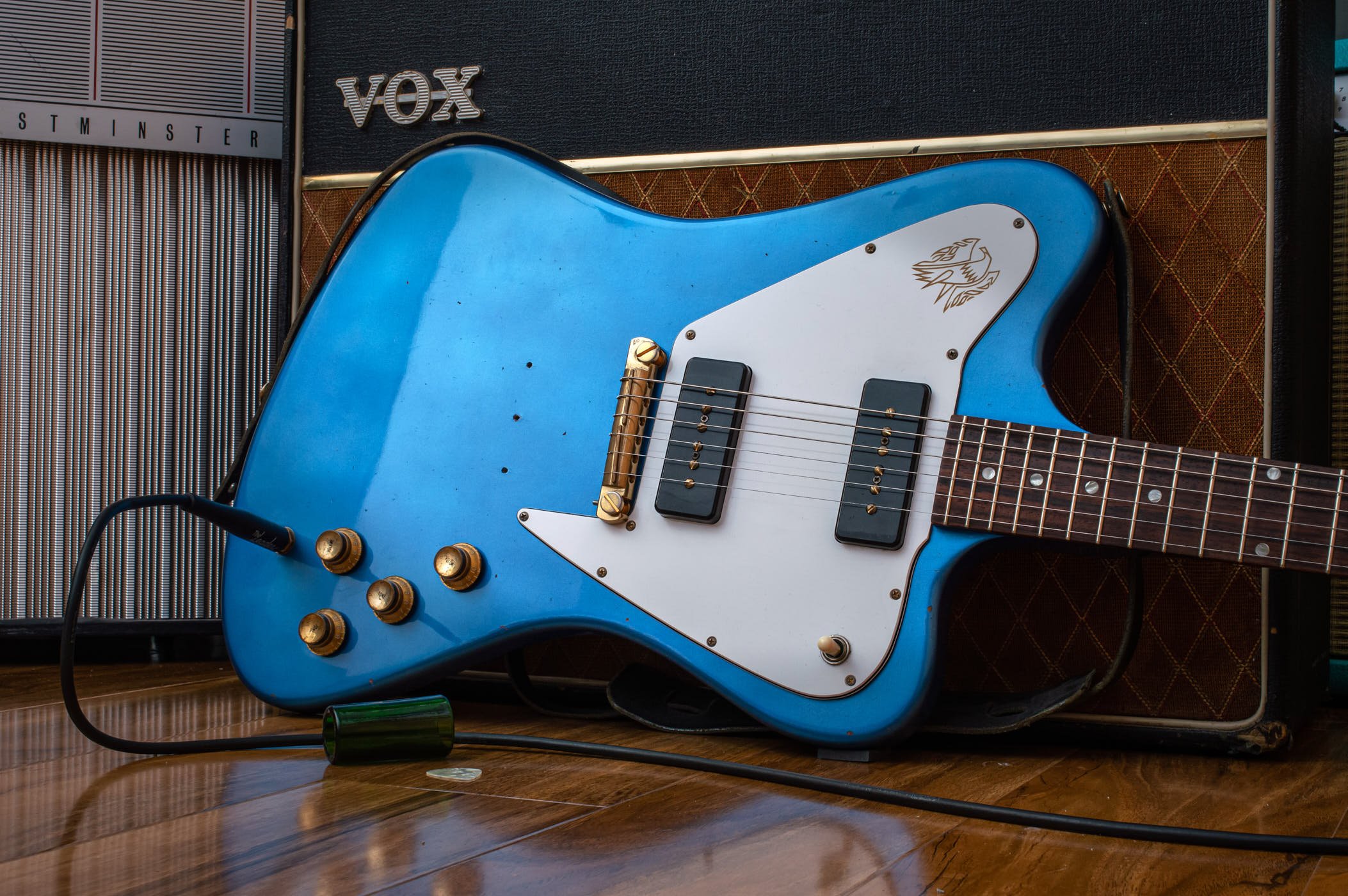
1965 Gibson Non-Reverse Firebird
This non-reverse Firebird had been so messed around and modified over the years, the owner and I weren’t even sure what model it was.
The only way to find out was to remove the lacquer from the front and search for bushing and screw holes.
What was intended to be a simple refinish and refret project turned out to be a full restoration, but this 1965 model from the first year of production was well worth the effort.
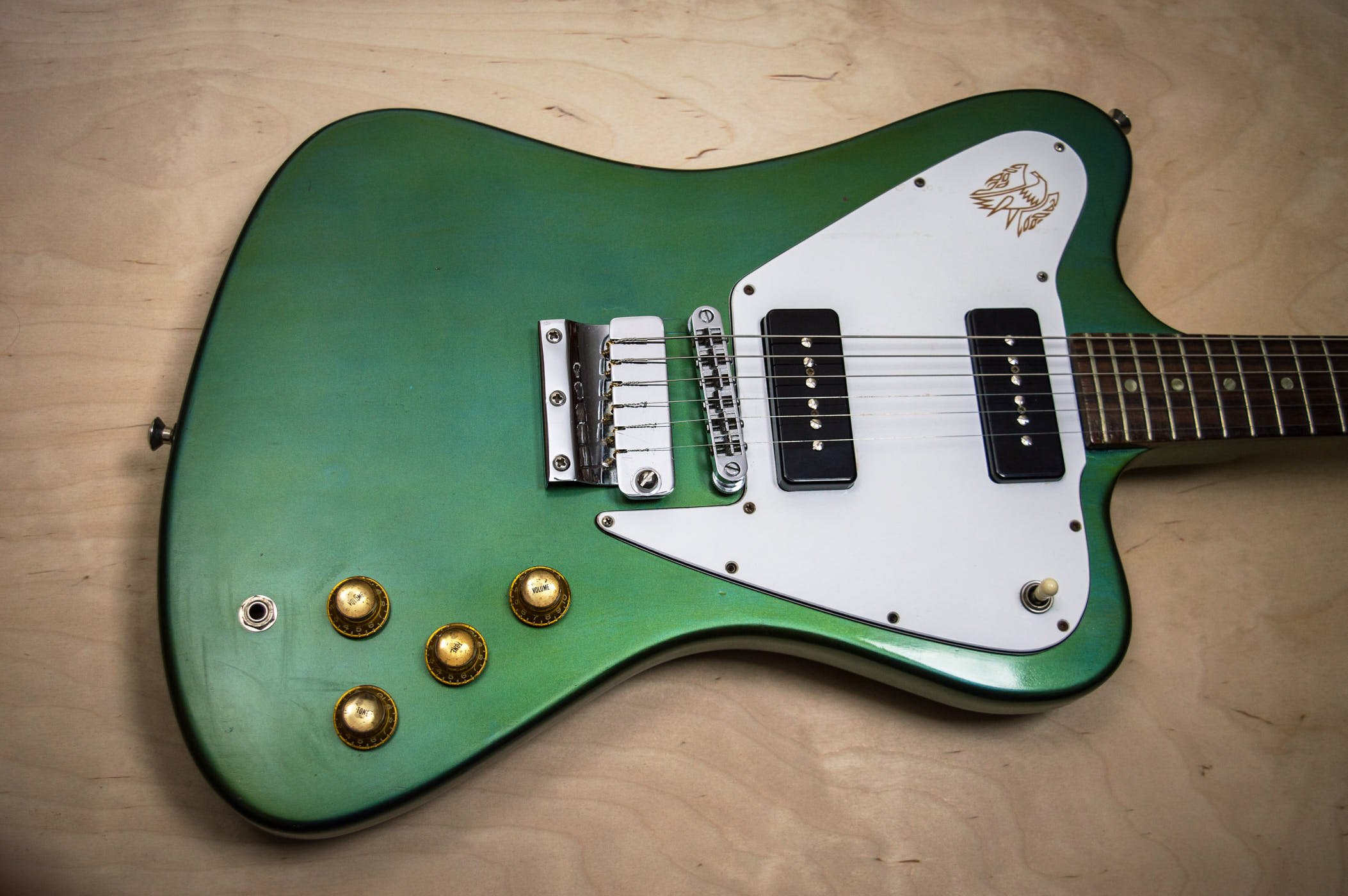
It arrived with lots of non-original parts and numerous plugged holes showing through a very green Pelham Blue refinish.
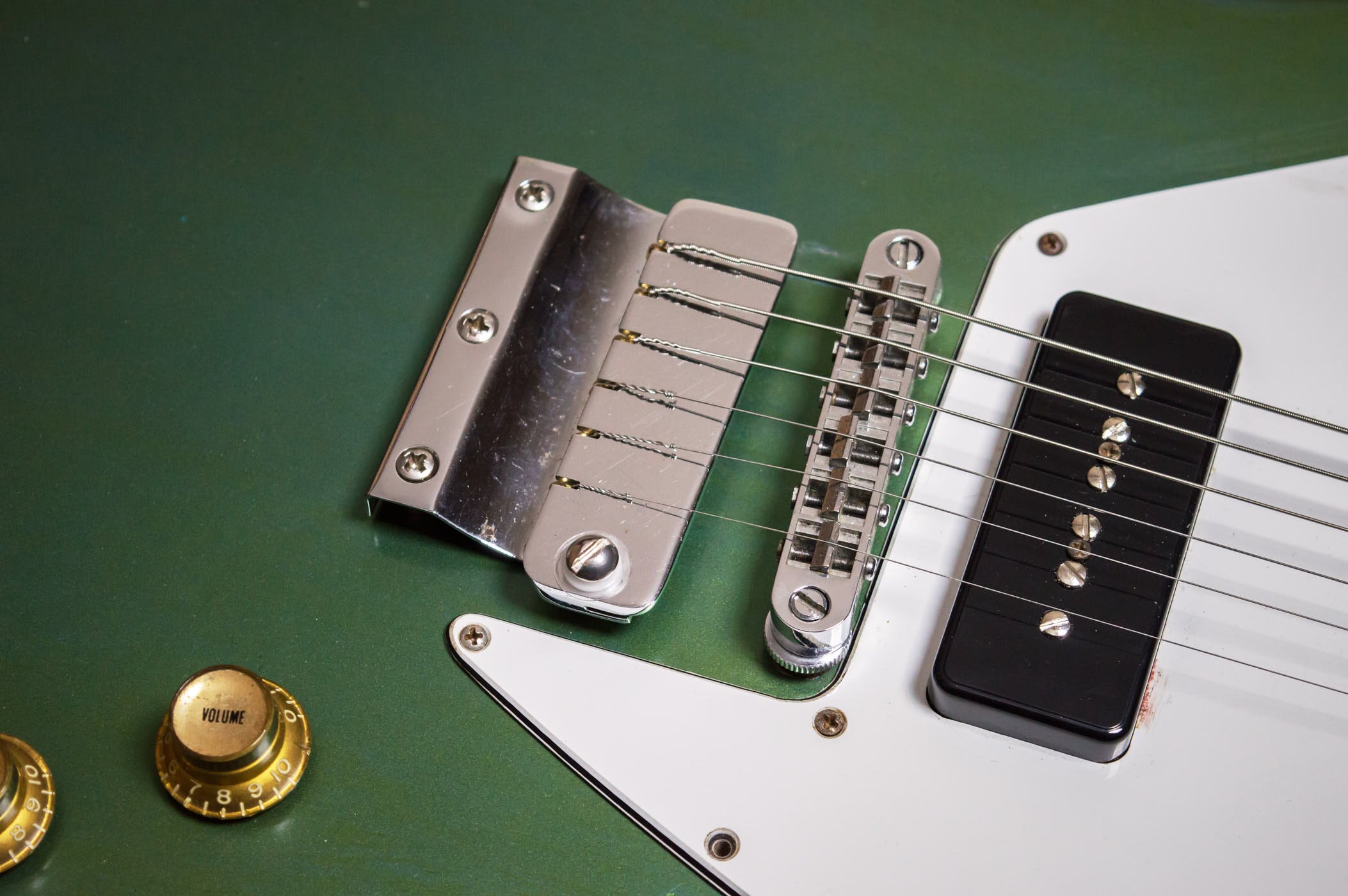
A Gotoh tune-o-matic style bridge has replaced the original unit, but at this stage it’s not certain what bridge was fitted at the factory.
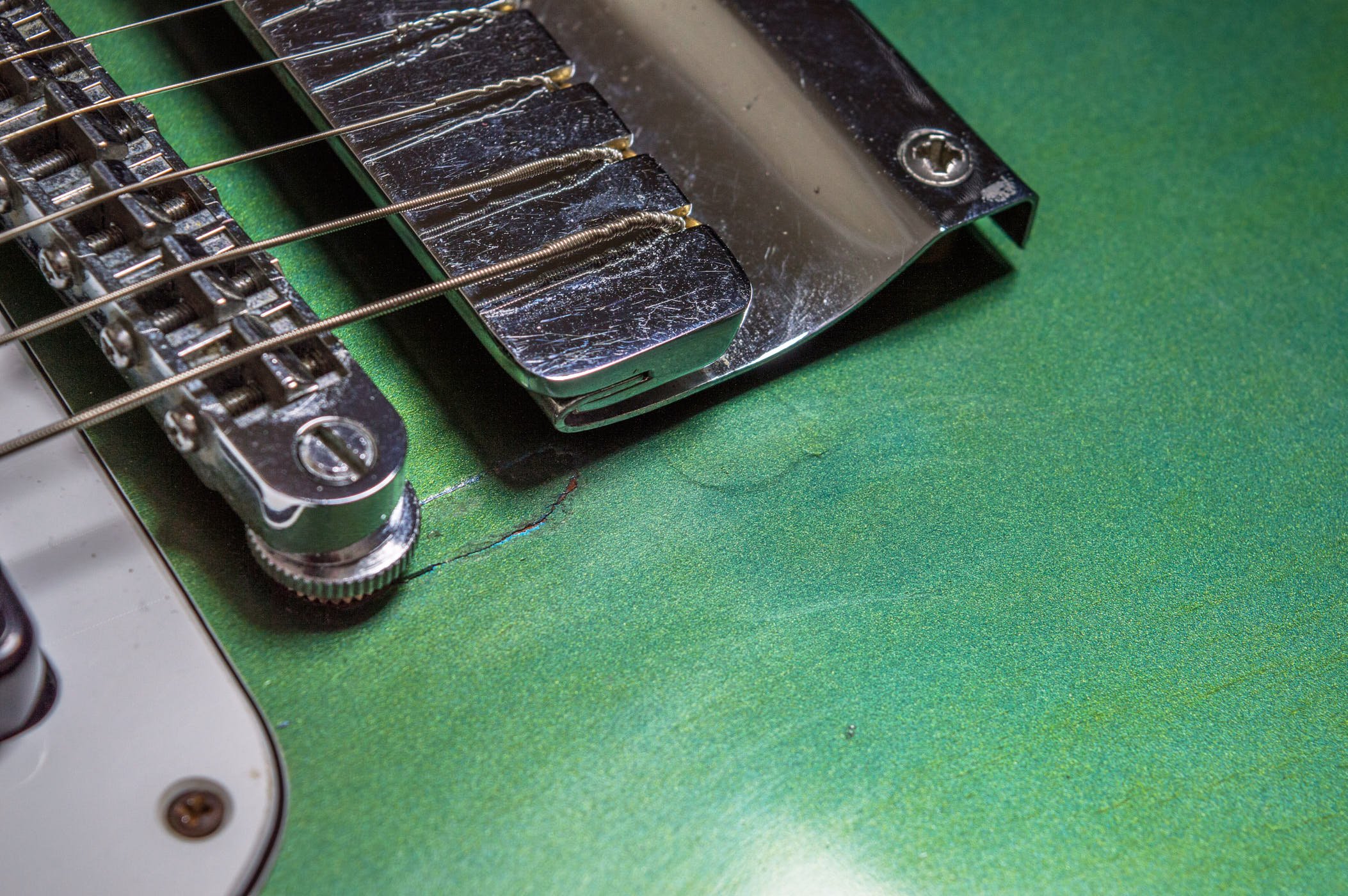
There’s some damage around the bass side bushing and a filled hole showing through the lacquer is evidence of a stop tailpiece.
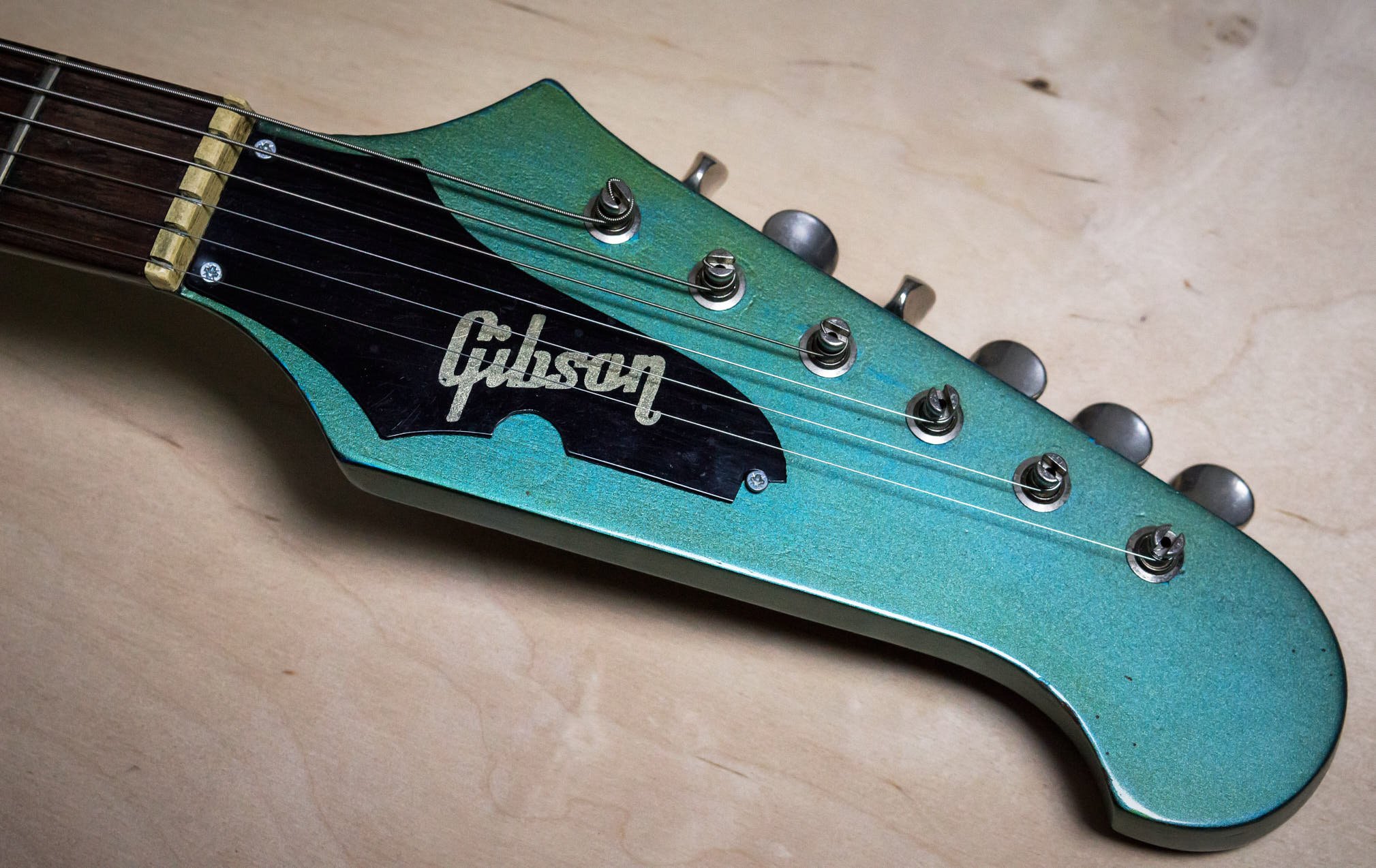
The headstock was modified for three-a-side tuners and although the holes have been plugged, the truss-rod cover still bears the scars.
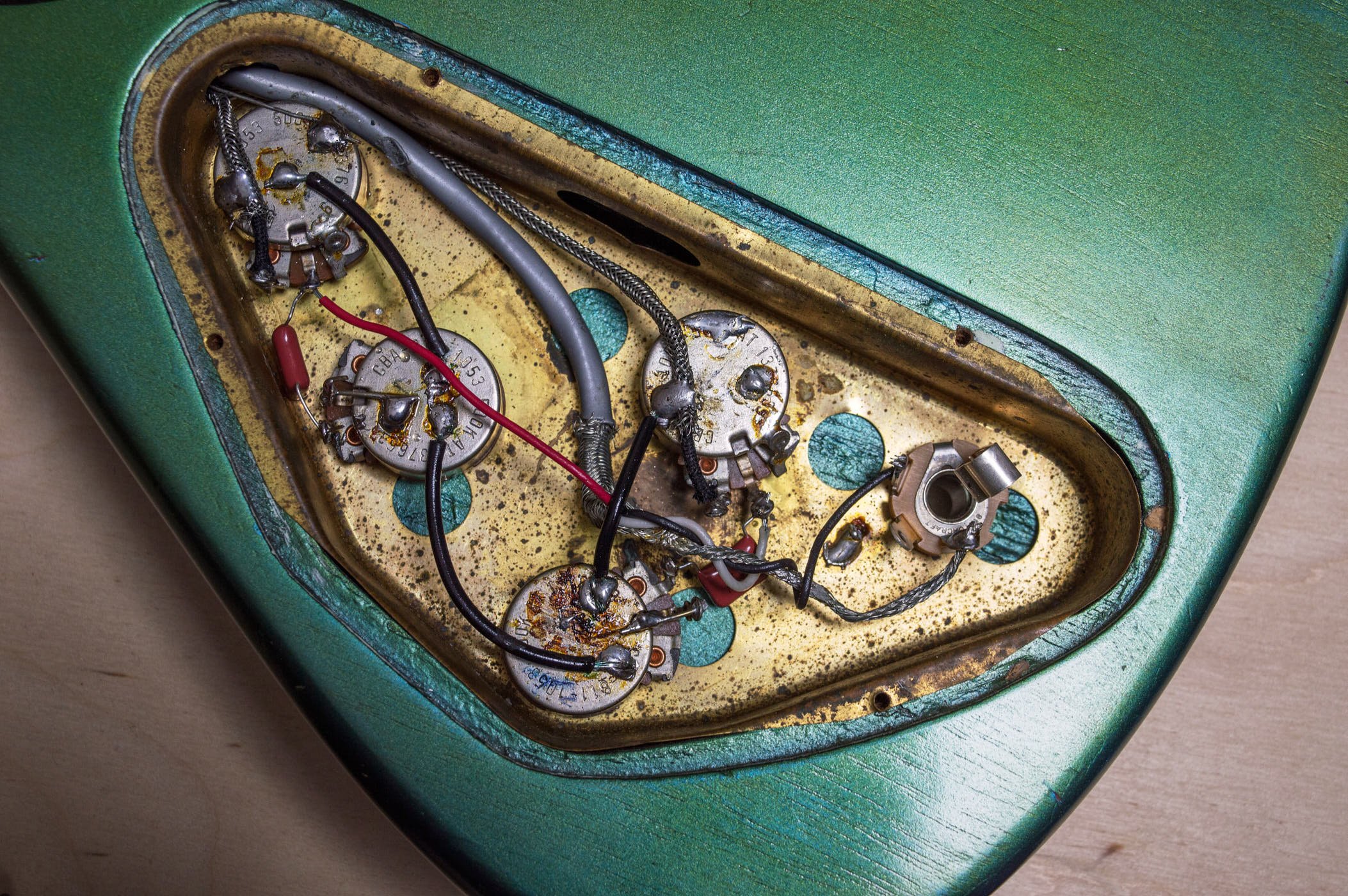
Besides the tone capacitors, all the controls and wiring are intact and the potentiometers date to 1965.
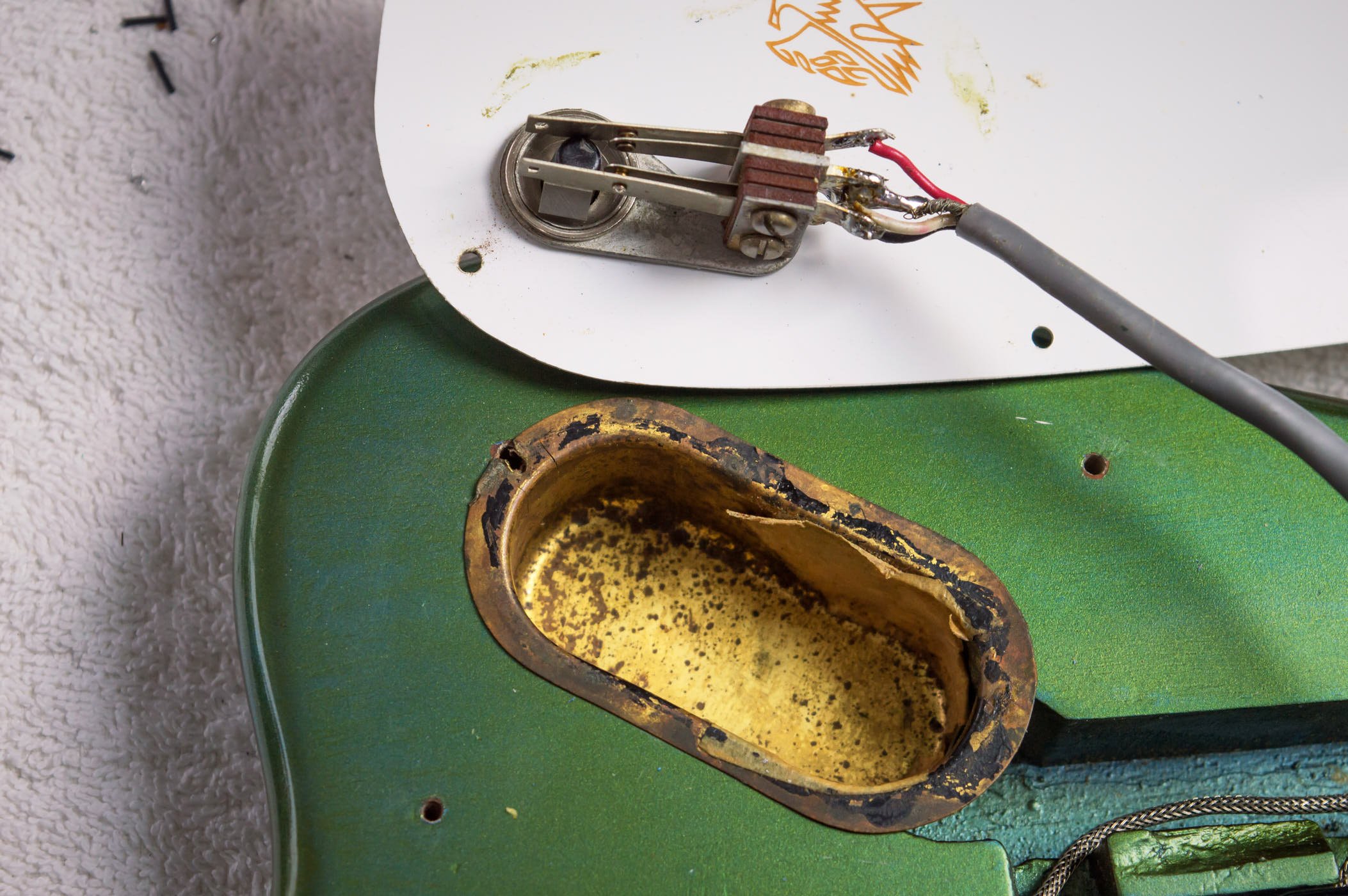
The toggle switch is old, but is it original? Most Non-Reverse Firebirds had slider switches.
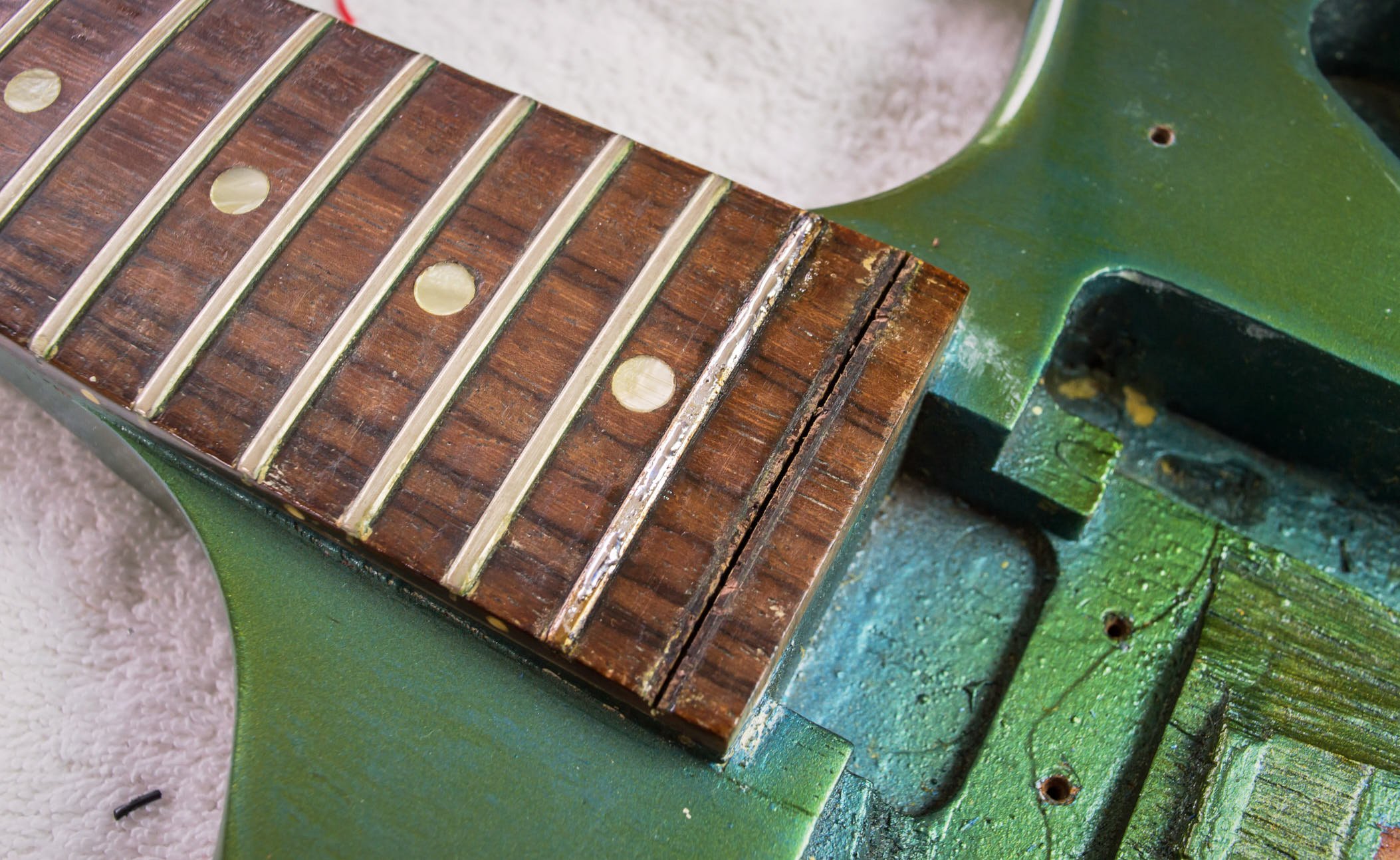
This guitar badly needed a refret here solder is being applied to conduct heat and melt the glue before extraction.
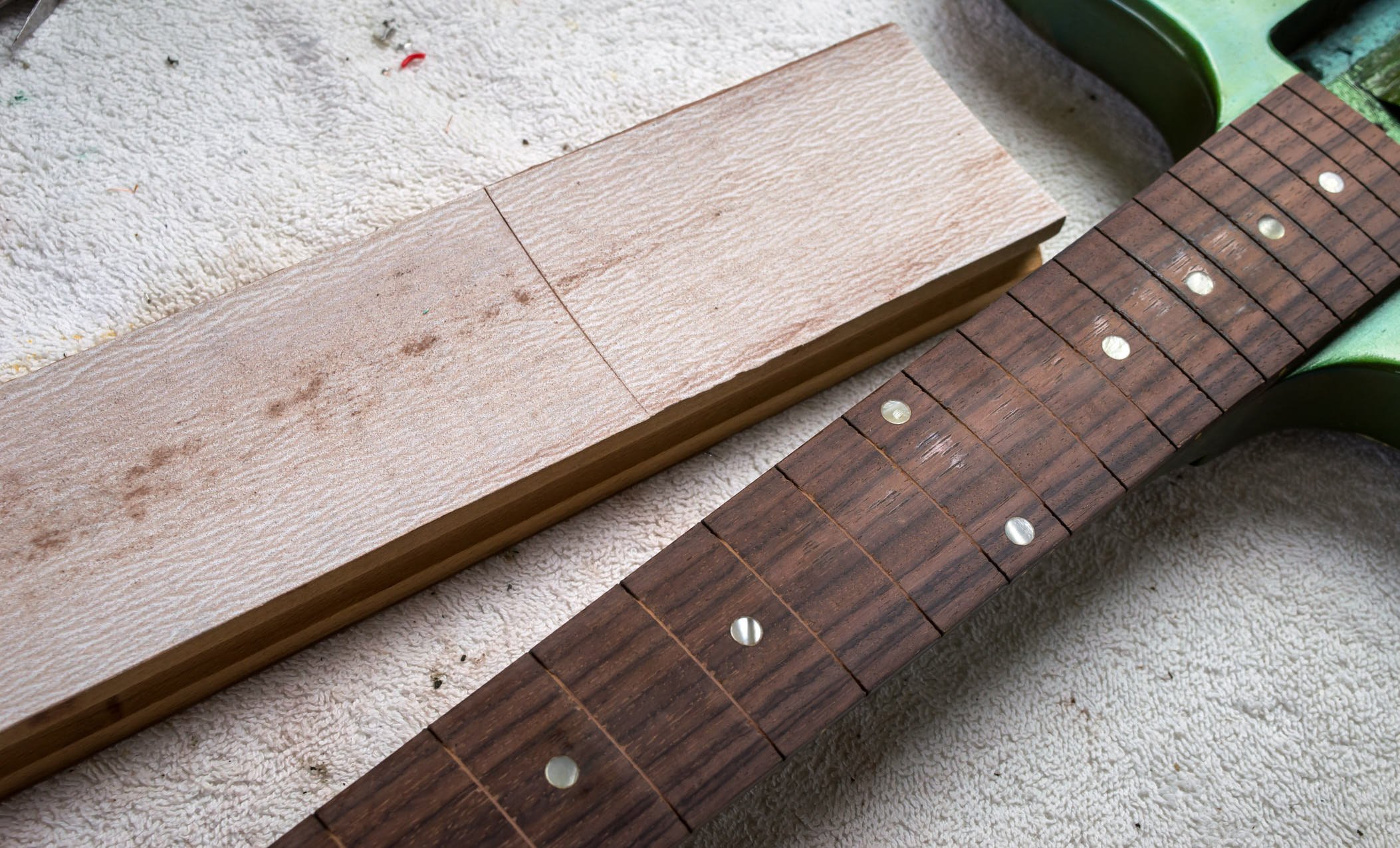
With all the frets removed a 9.5-inch radius block is used to level the fretboard and remove all traces of varnish.
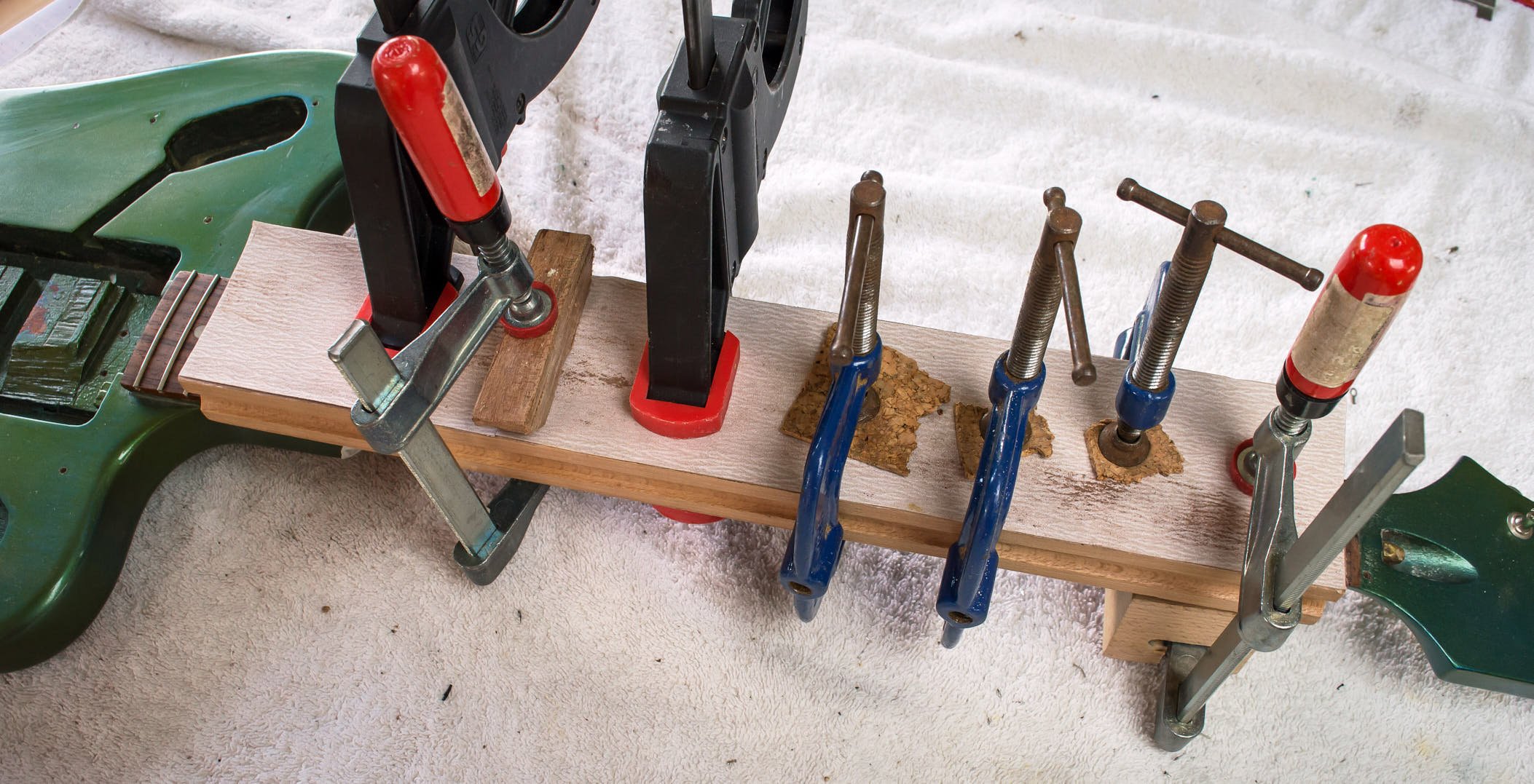
The new frets are pressed in with fish glue, and the radius block is clamped over the frets to hold them in position as the glue dries.
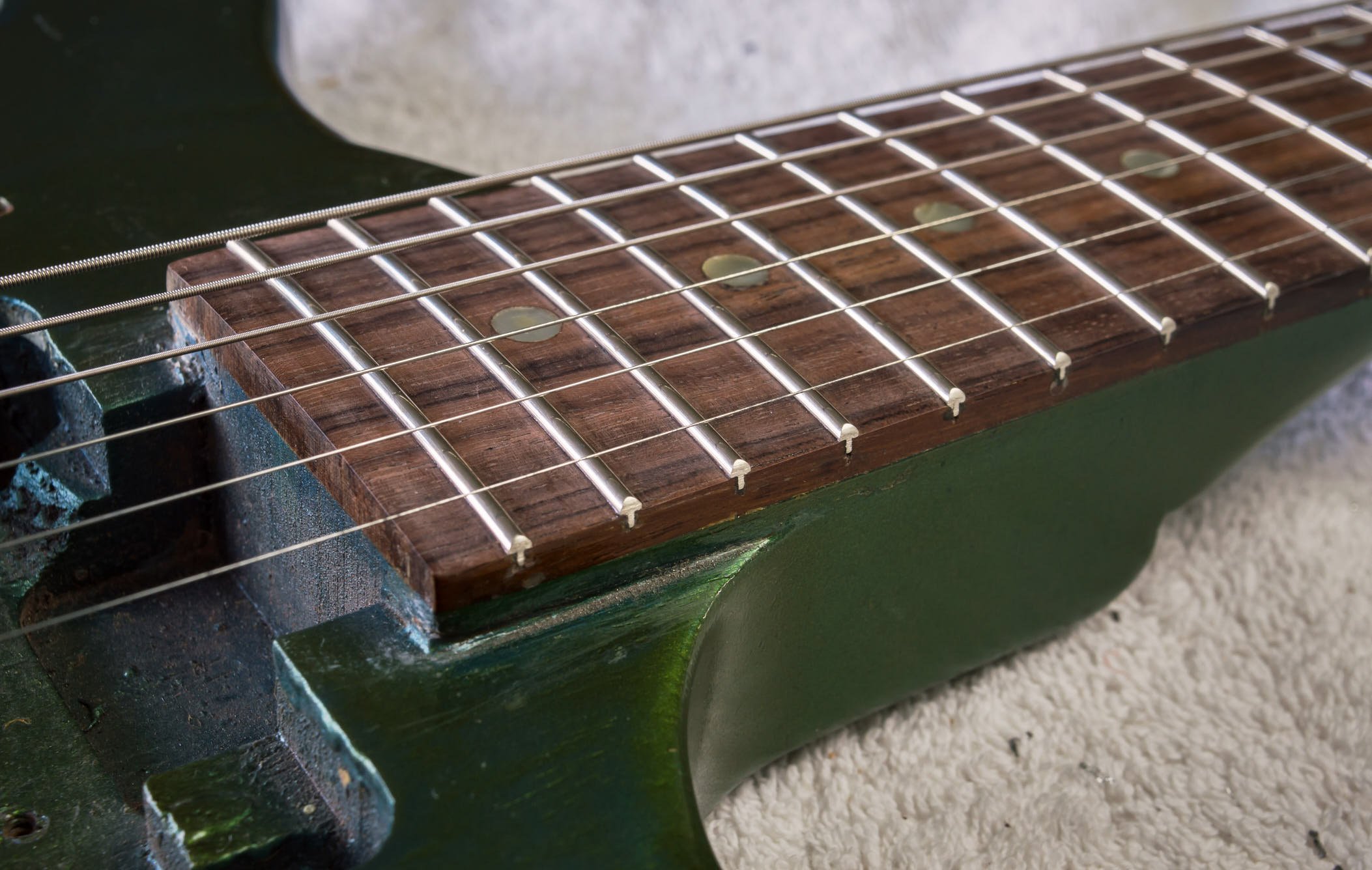
These fret ends have been bevelled but are not yet rounded or polished when the guitar is strung up for testing.
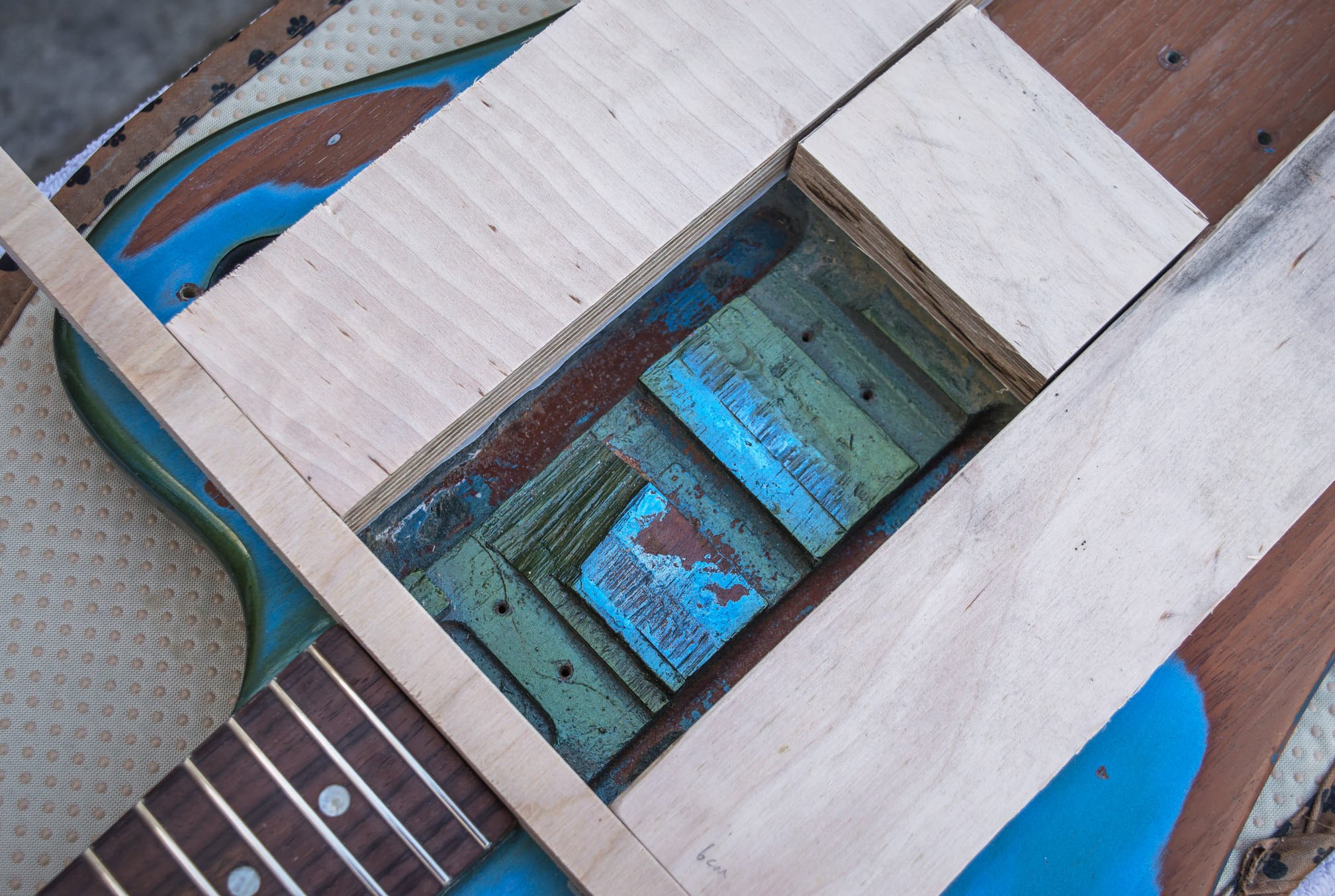
First year non-reverse Firebird I models had routed platforms to support the P90 pickups, but these were crudely chiselled off to accommodate a pair of full size humbuckers.
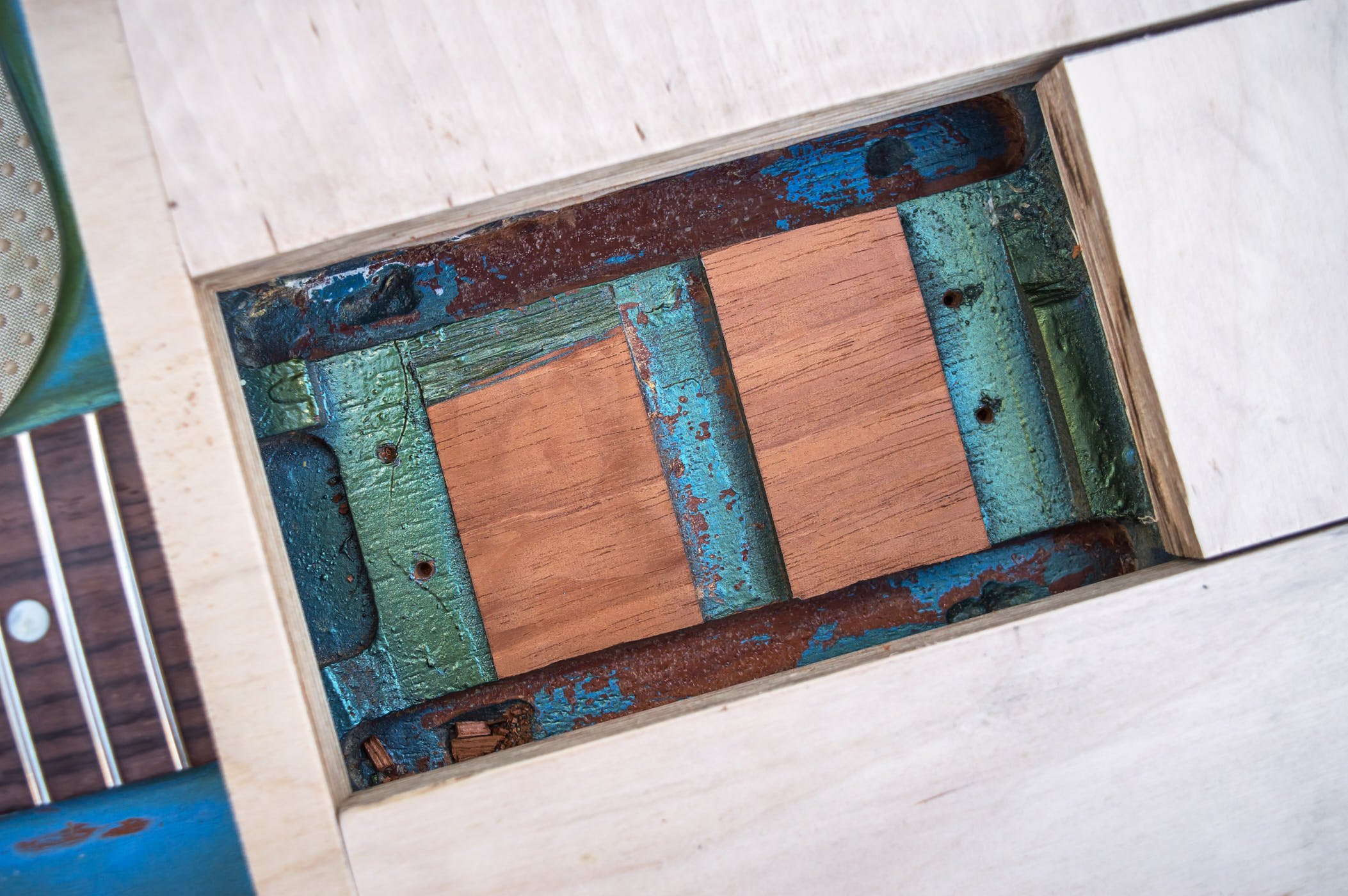
A router is used to tidy up the chipped area and provide a flat surface for gluing.
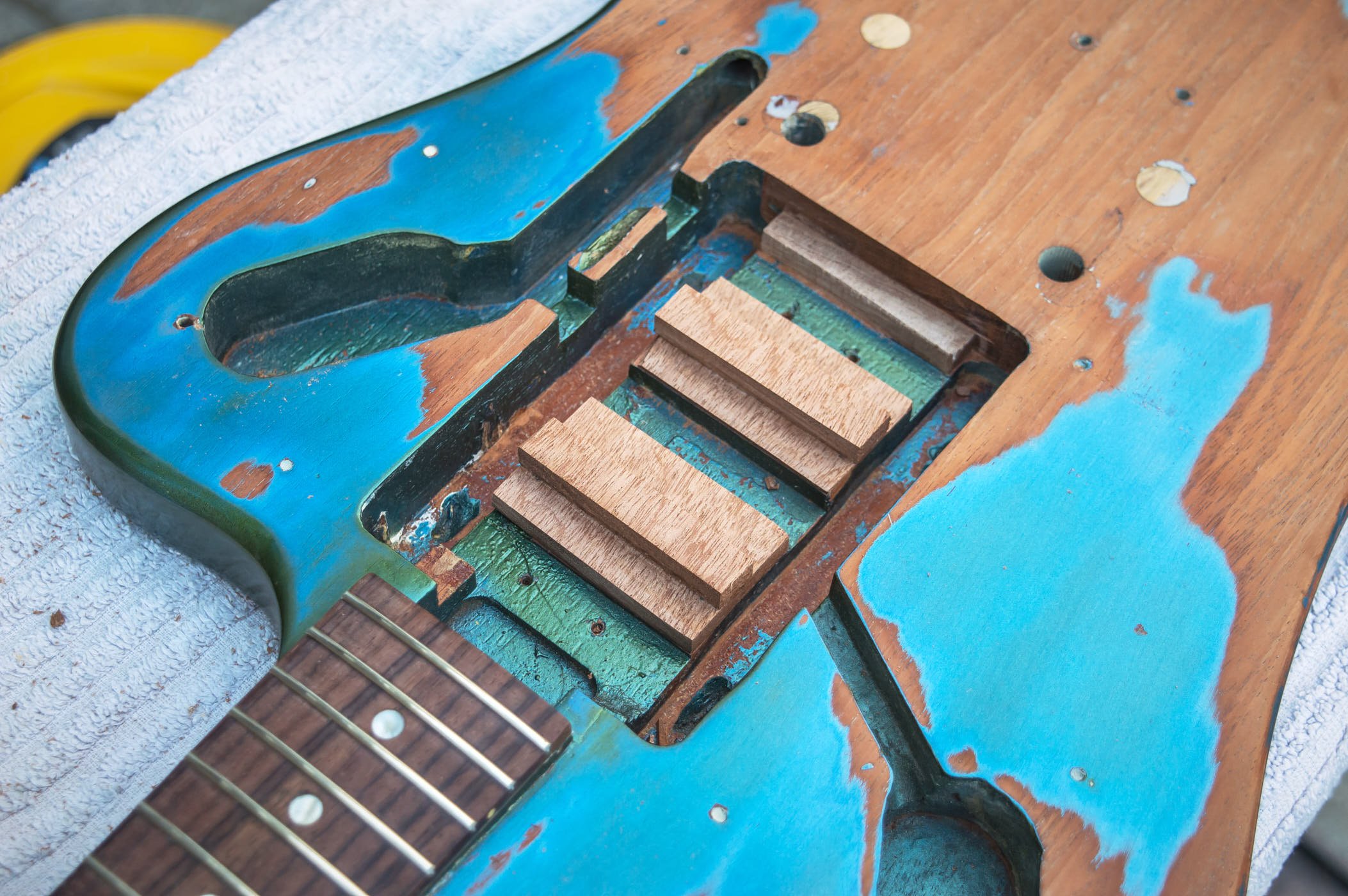
Mahogany blocks are glued in to restore the original appearance and make it as difficult as possible for anybody to attempt a humbucker conversion in the future.

With the Gotoh bridge bushing removed, you can see the maple dowel and flat-sawn mahogany plug that was used to fill the original wraptail bushing hole.
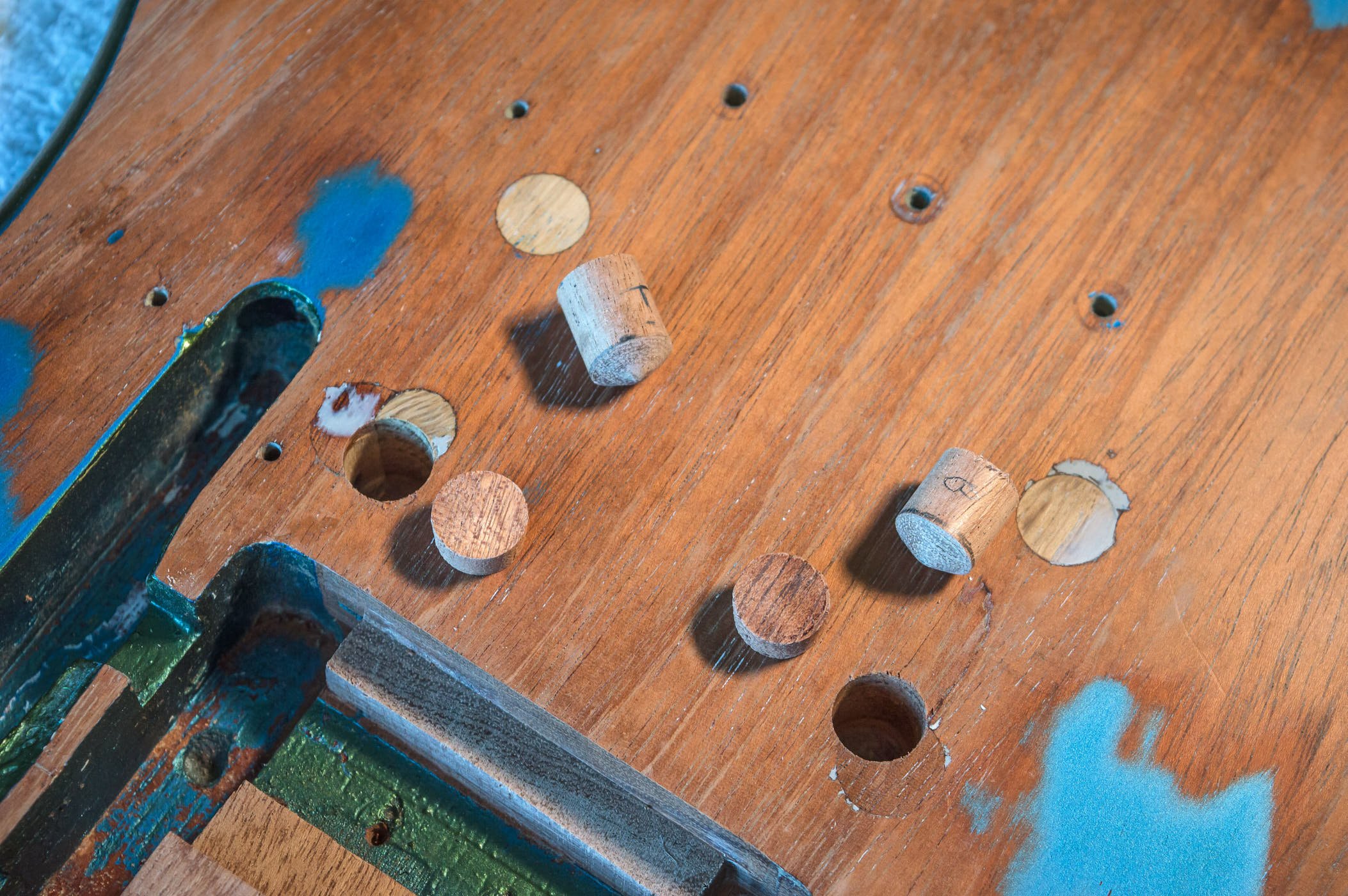
Mahogany dowels are shaped and cut to length to fill the tune-o-matic bushing holes, and they’ll be capped with these flat sawn mahogany plugs.
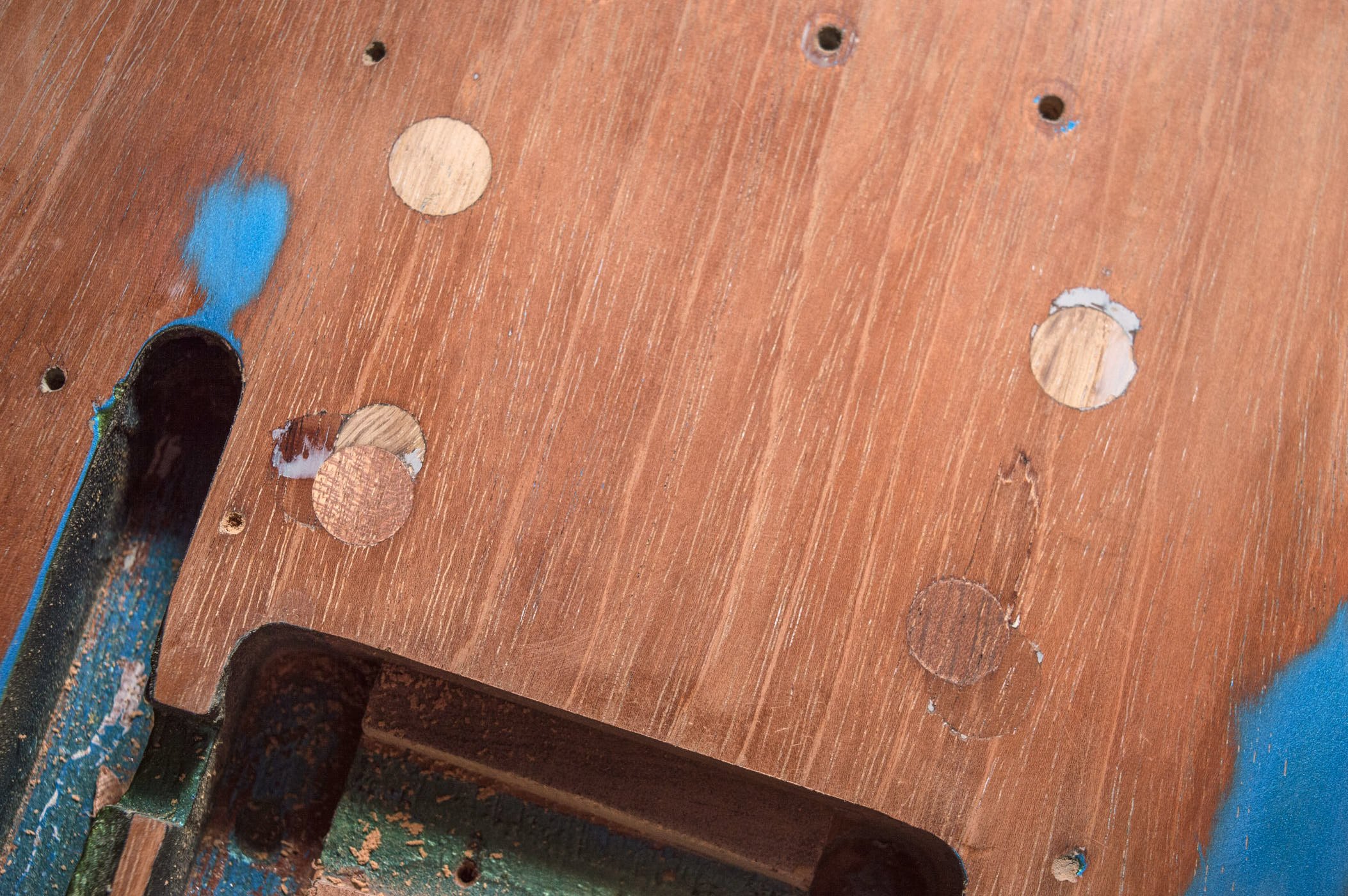
All the holes have been plugged - seven in total - and this Firebird 1 is now ready for a wraptail once again.
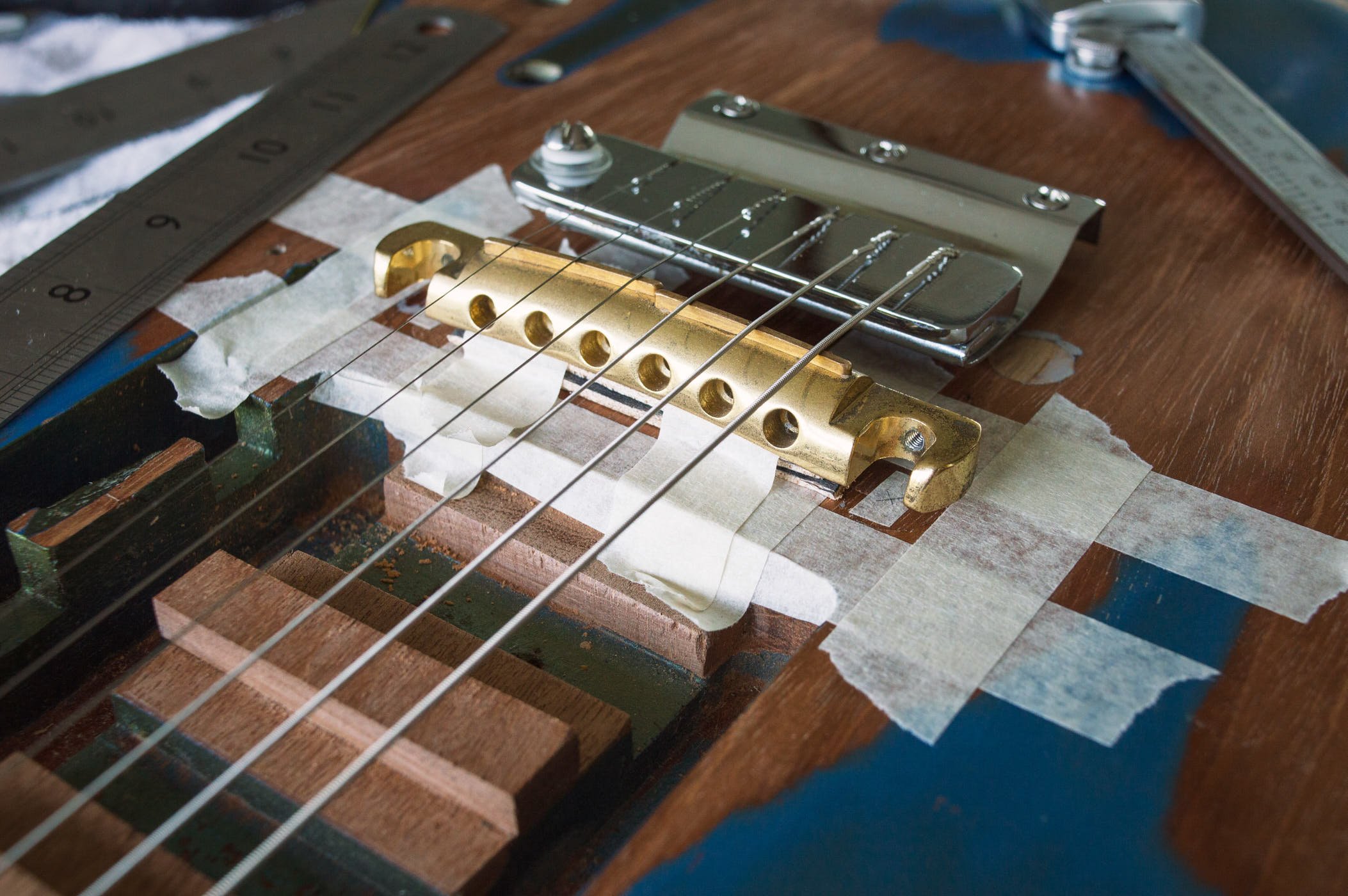
With the Vibrola anchoring the strings, the new wraptail is shimmed on veneer strips and carefully moved into position.
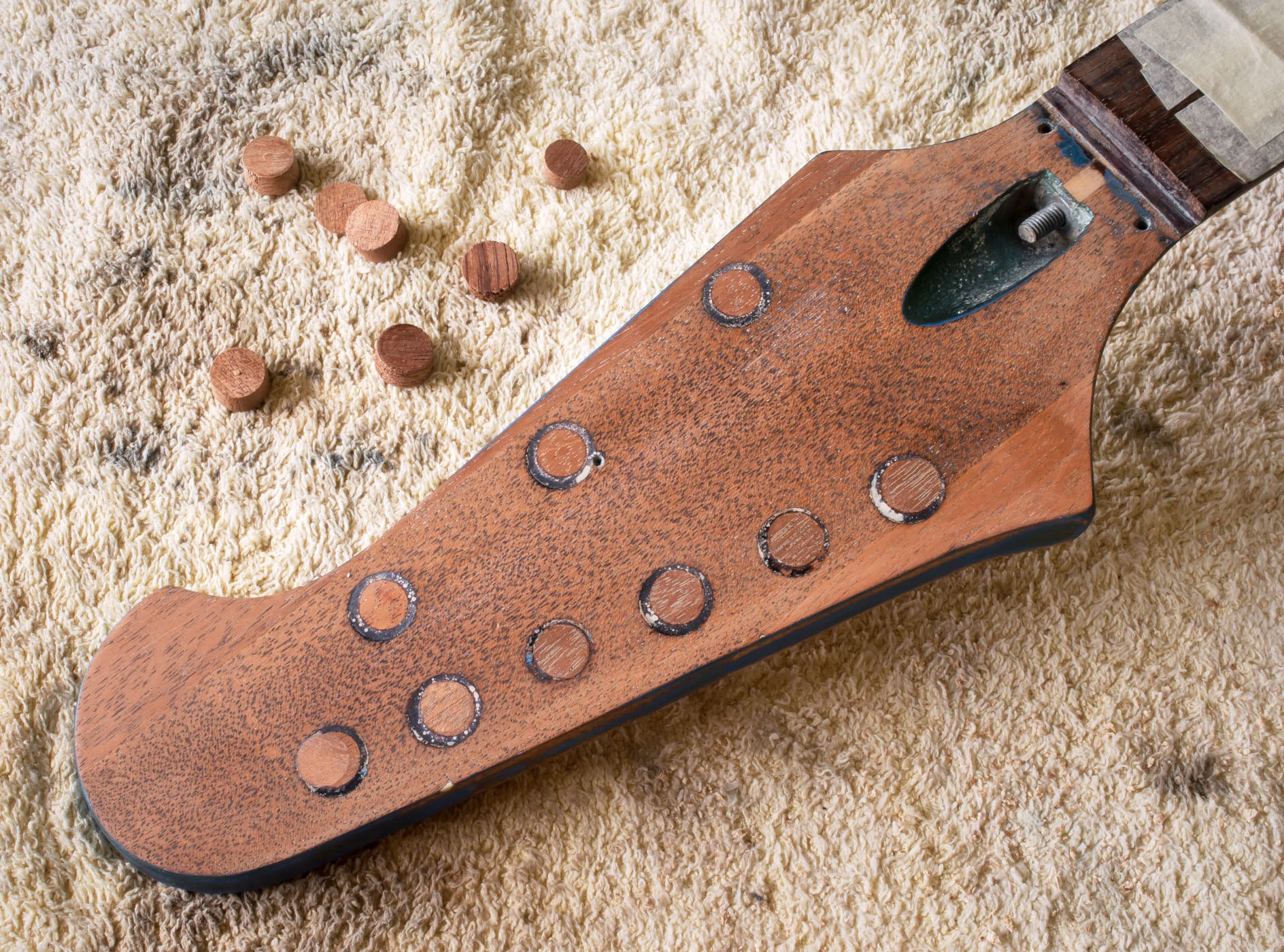
All the flat sawn plugs in the front of the headstock have been glued in and levelled.
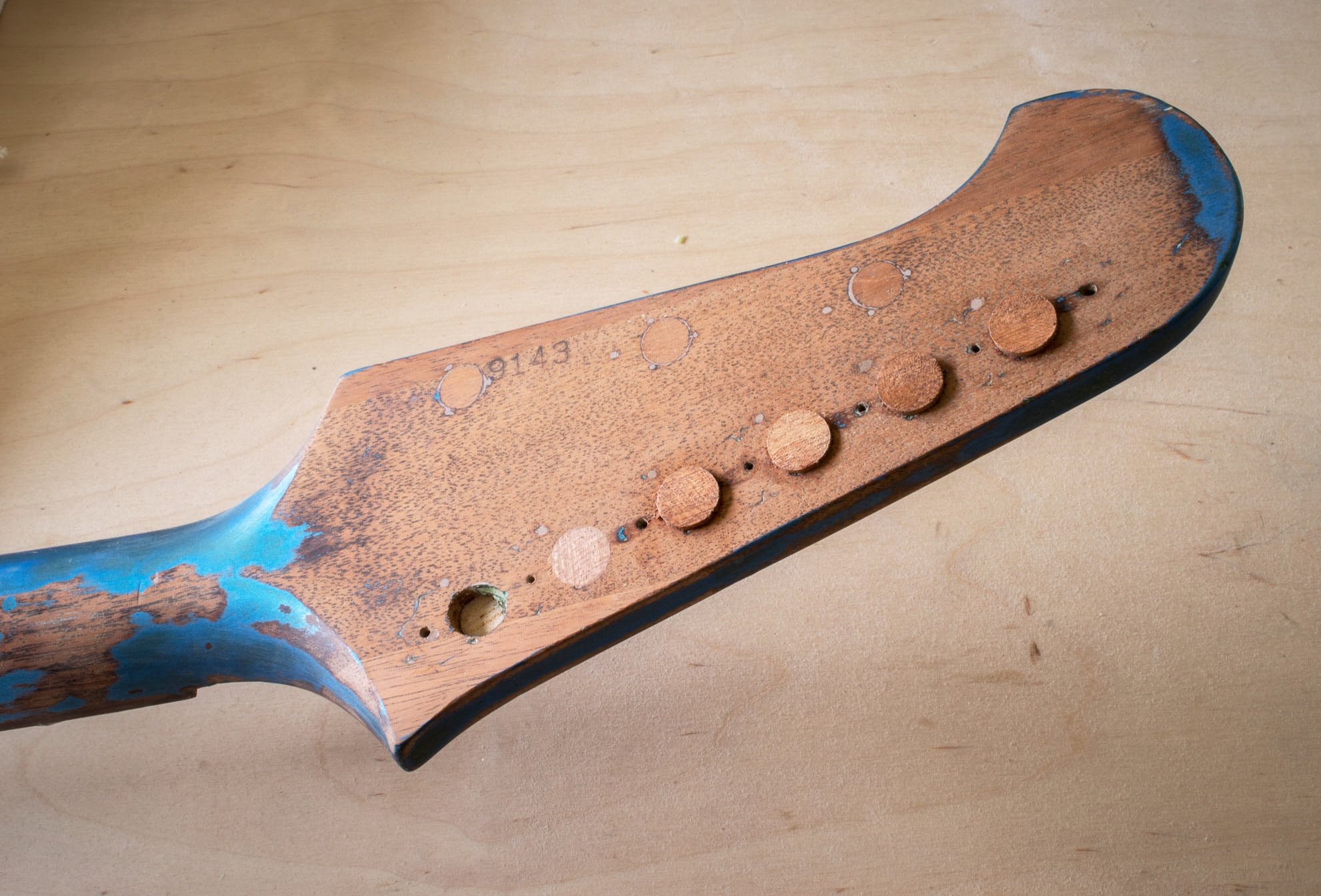
Five of the rear plugs have been installed and one has been levelled, so there’s only one more to go.
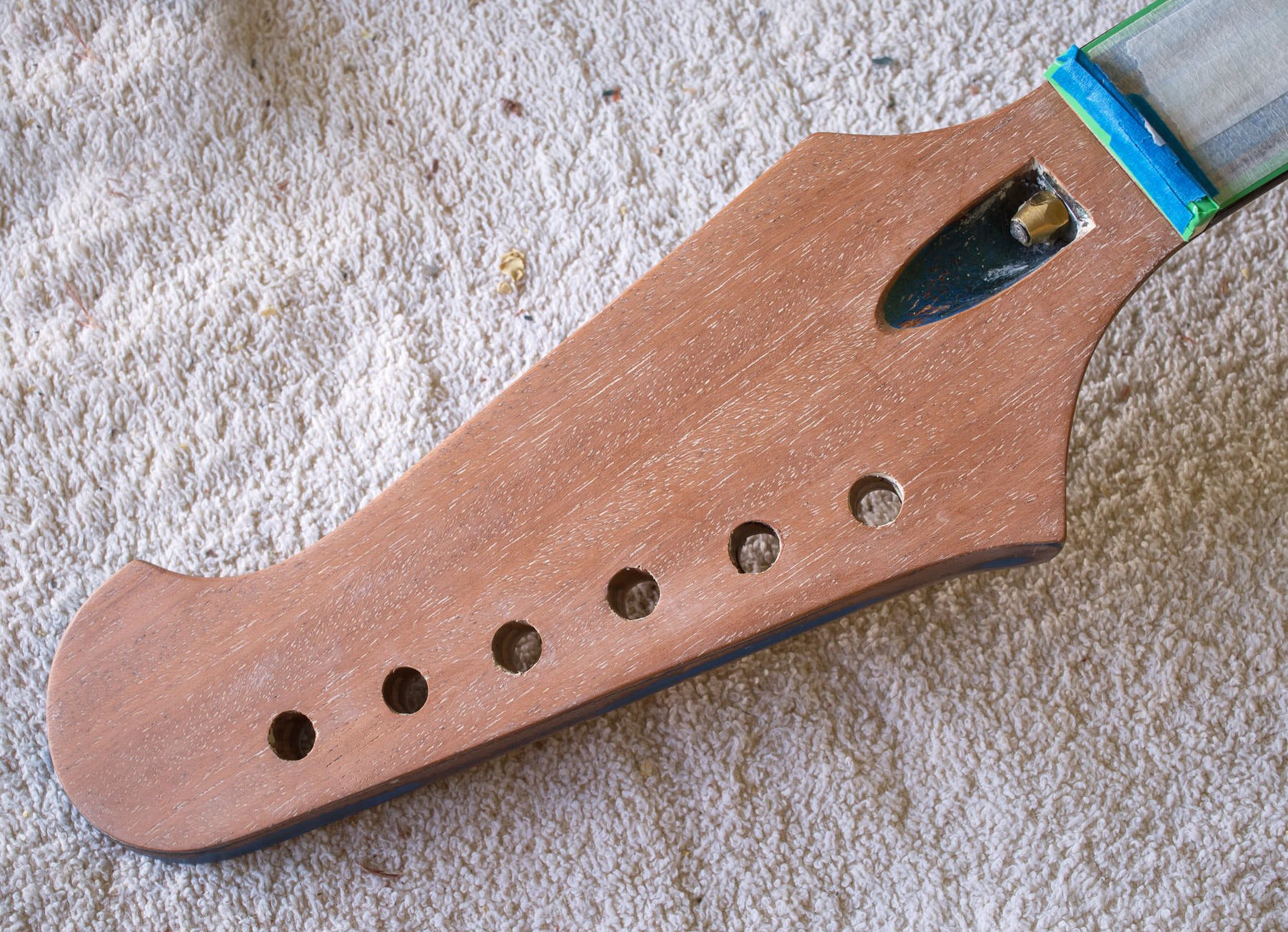
To prevent the repairs showing through the finish, I’ve veneered the headstock face with mahogany and drilled new holes for six-on-a-strip Kluson style tuners.
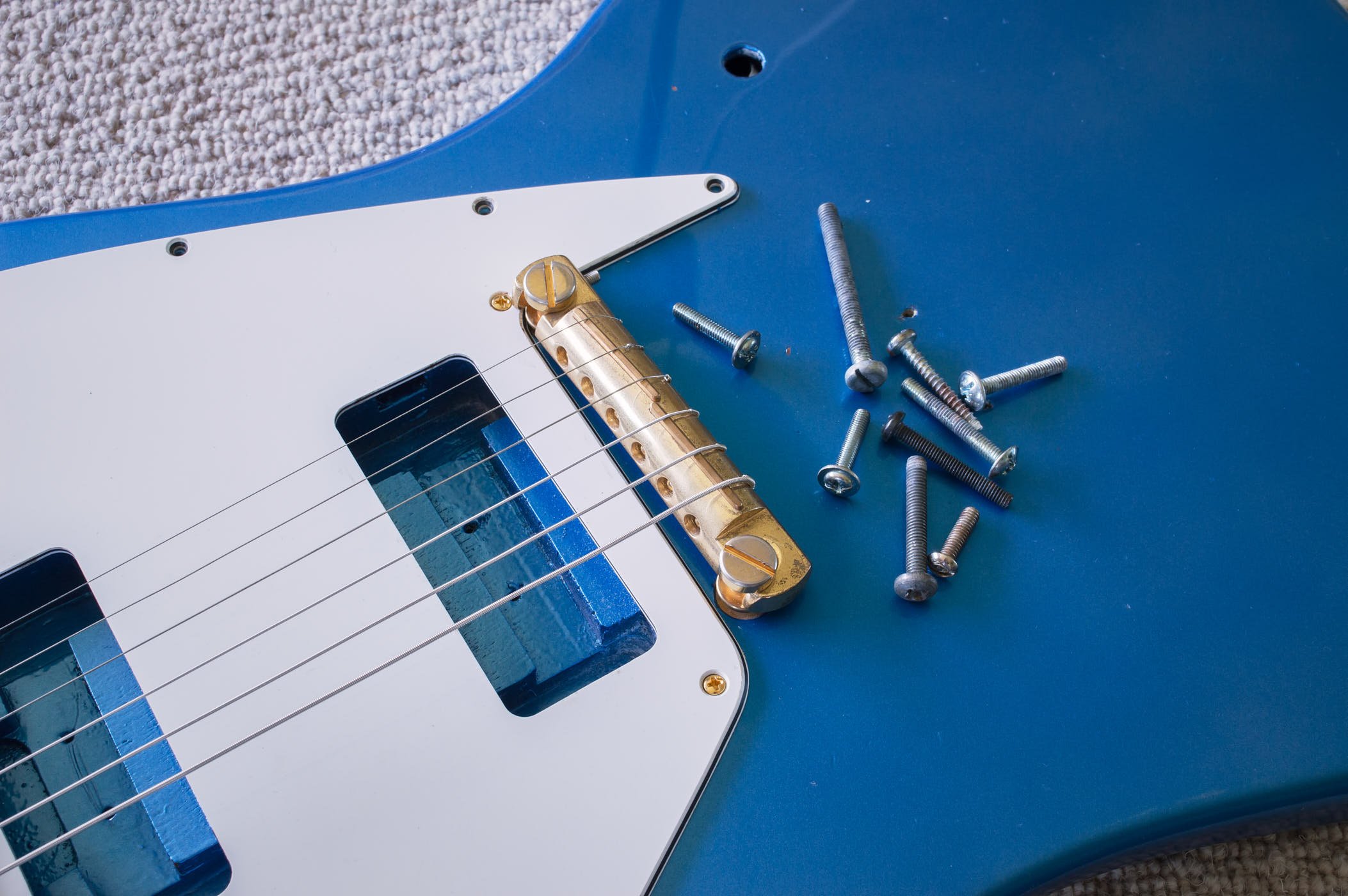
The owner specified a light ageing job so, in order to dent the finish, medium-sized bolts are dropped onto the surface rather than bunches of keys.
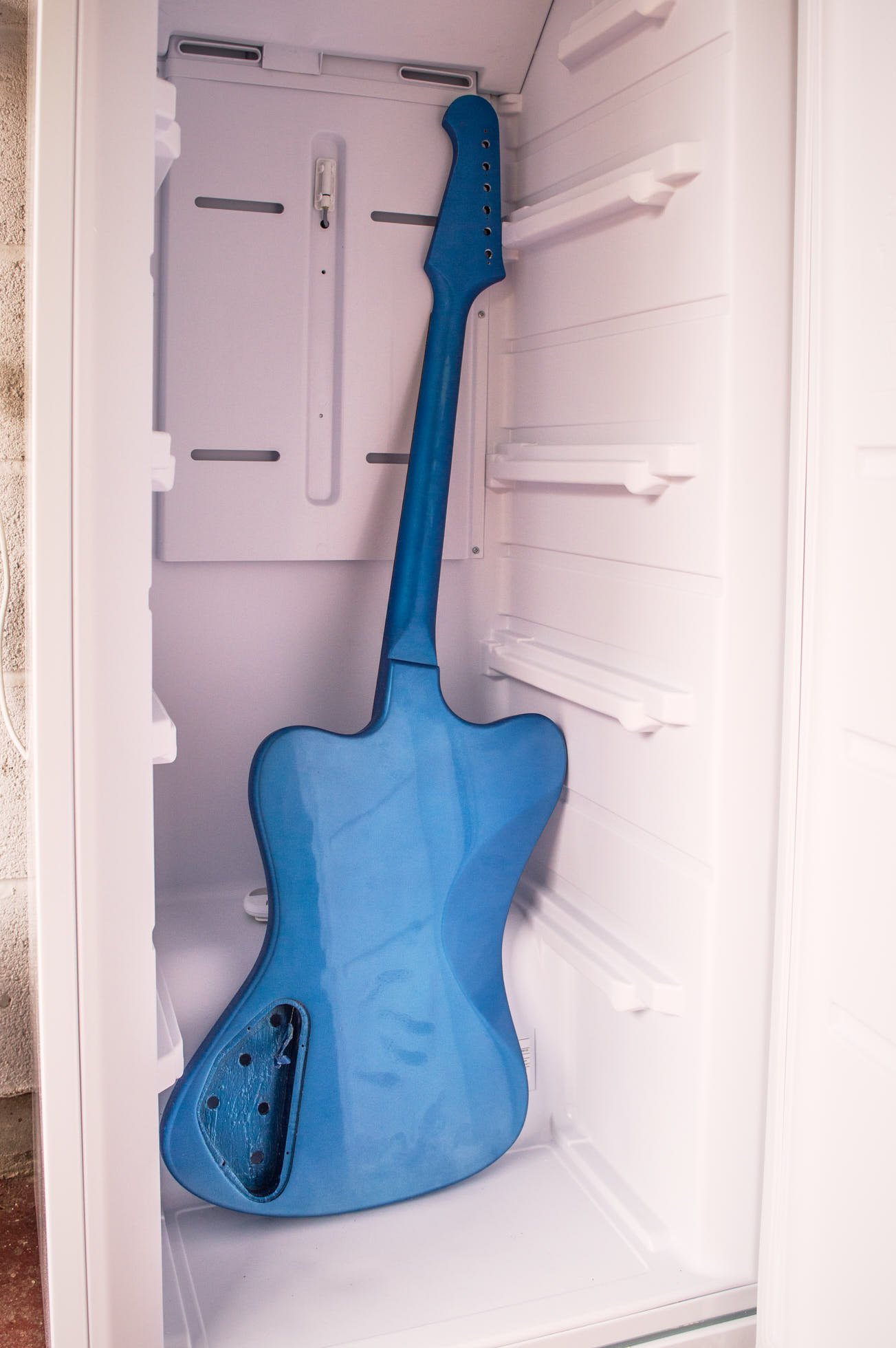
You need a sizeable deep freeze for a set-neck guitar – and Firebirds in particular – but it’s the best way to induce lacquer checking.
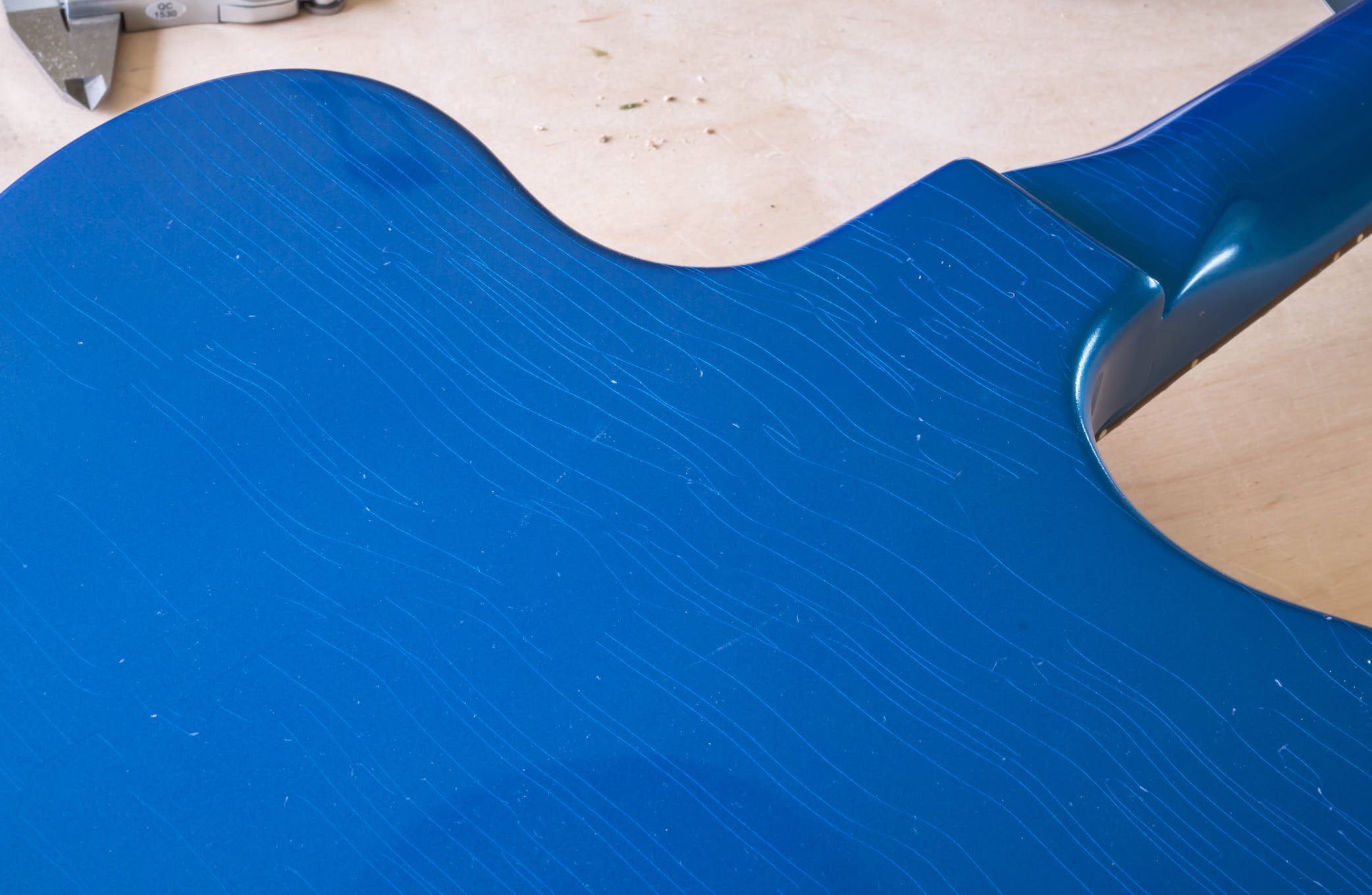
After three freeze and thaw cycles, checking lines have formed all over the the non-tinted Pelham Blue finish.
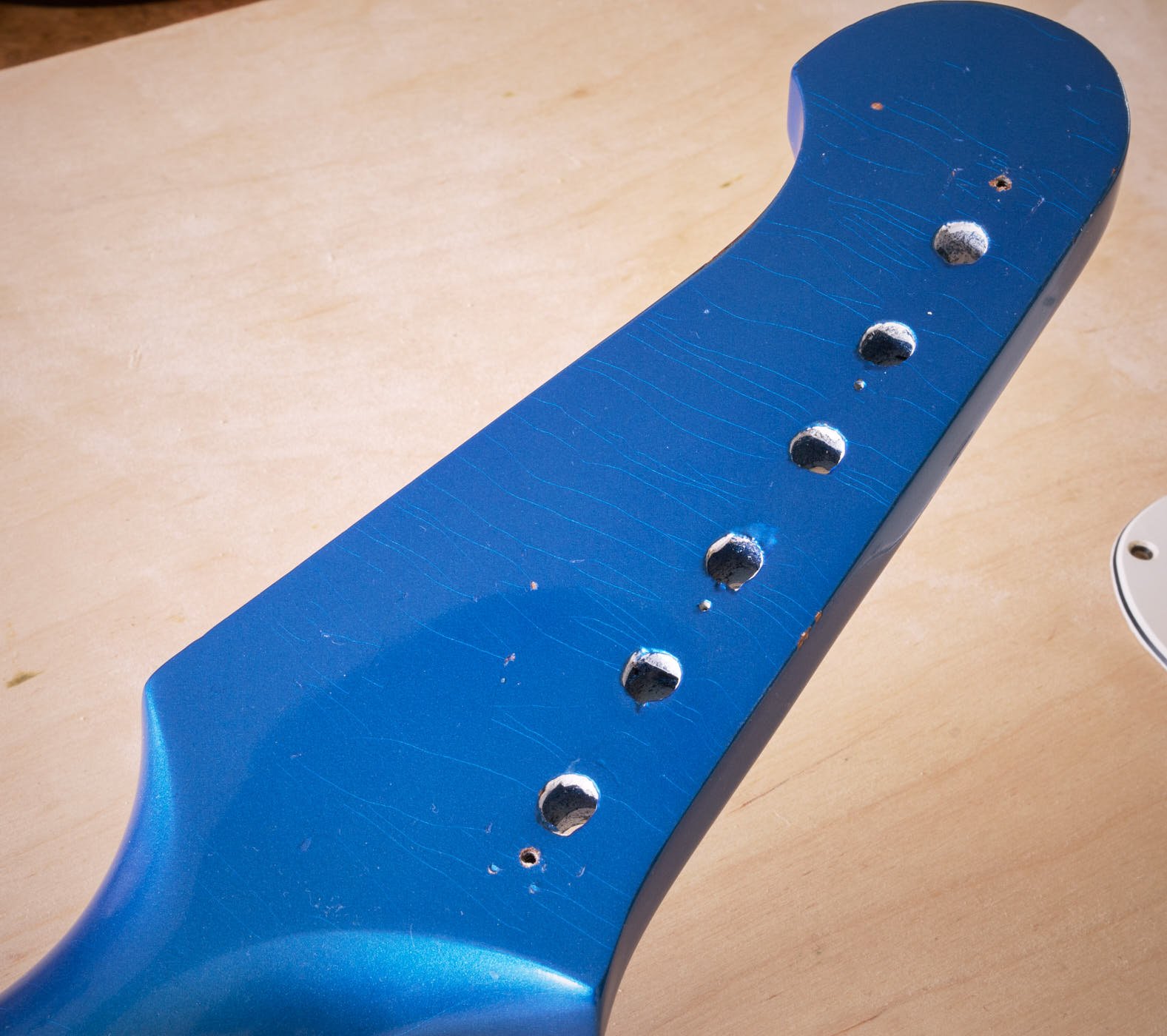
So far no pugs are showing through the finish, but that might change as the lacquer shrinks back over the next few years.
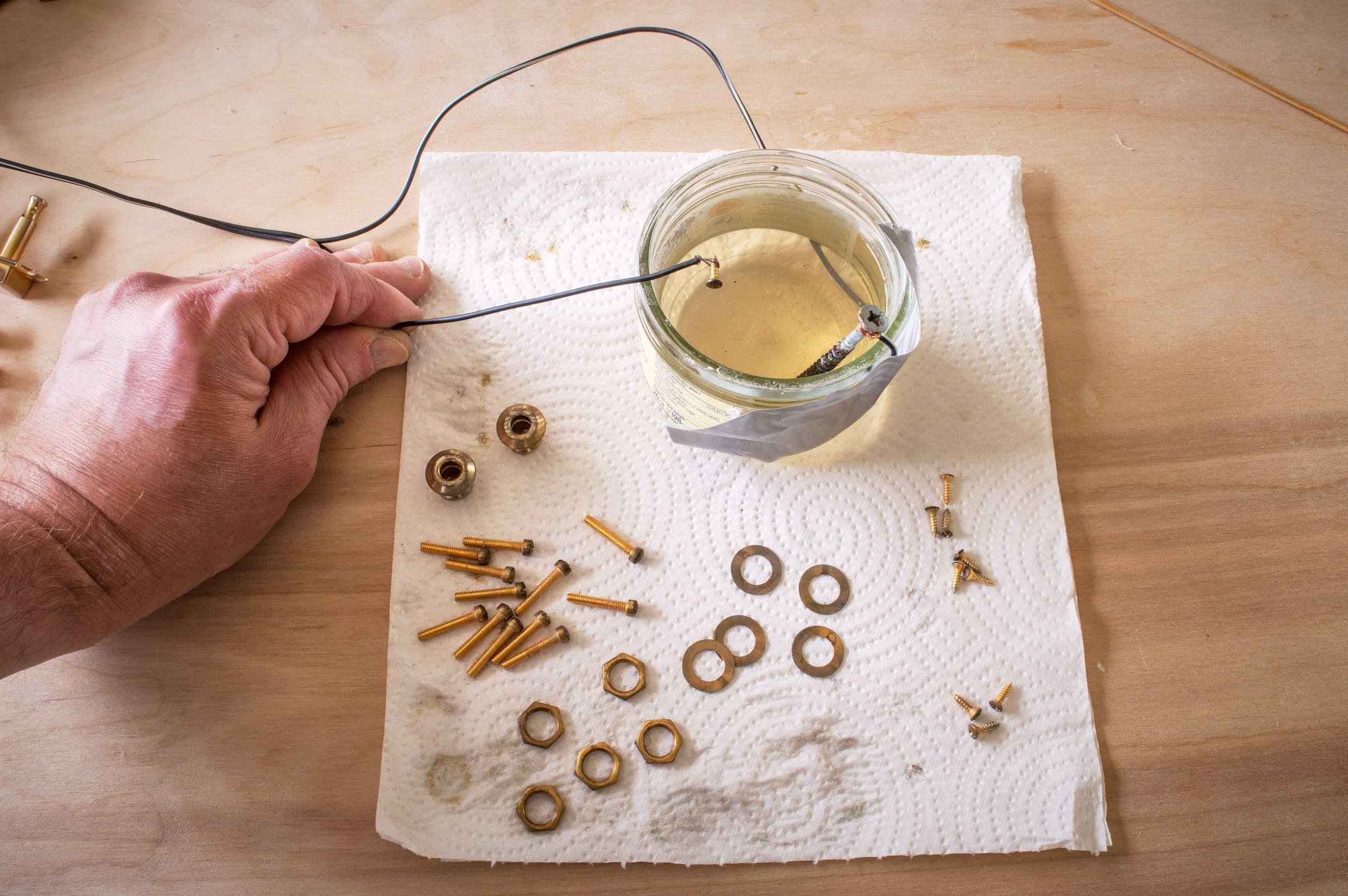
The owner specified aged gold hardware so after rubbing down with a Brasso pad, a 9v transformer and a jar of salty water finishes the relic’ing process.
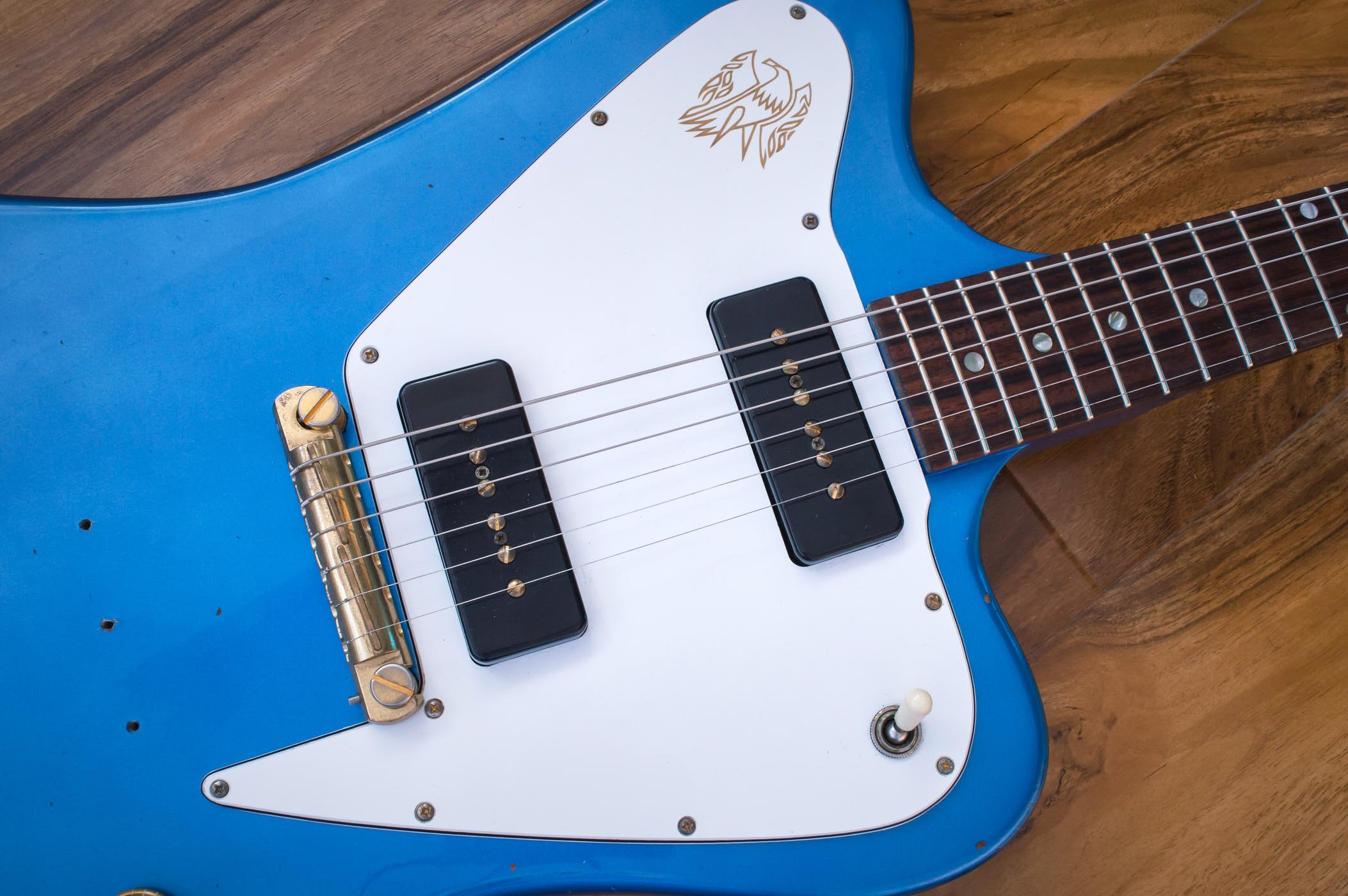
It was decided to keep the Vibrola off the body, but the holes are there and it can be reinstalled at any time.
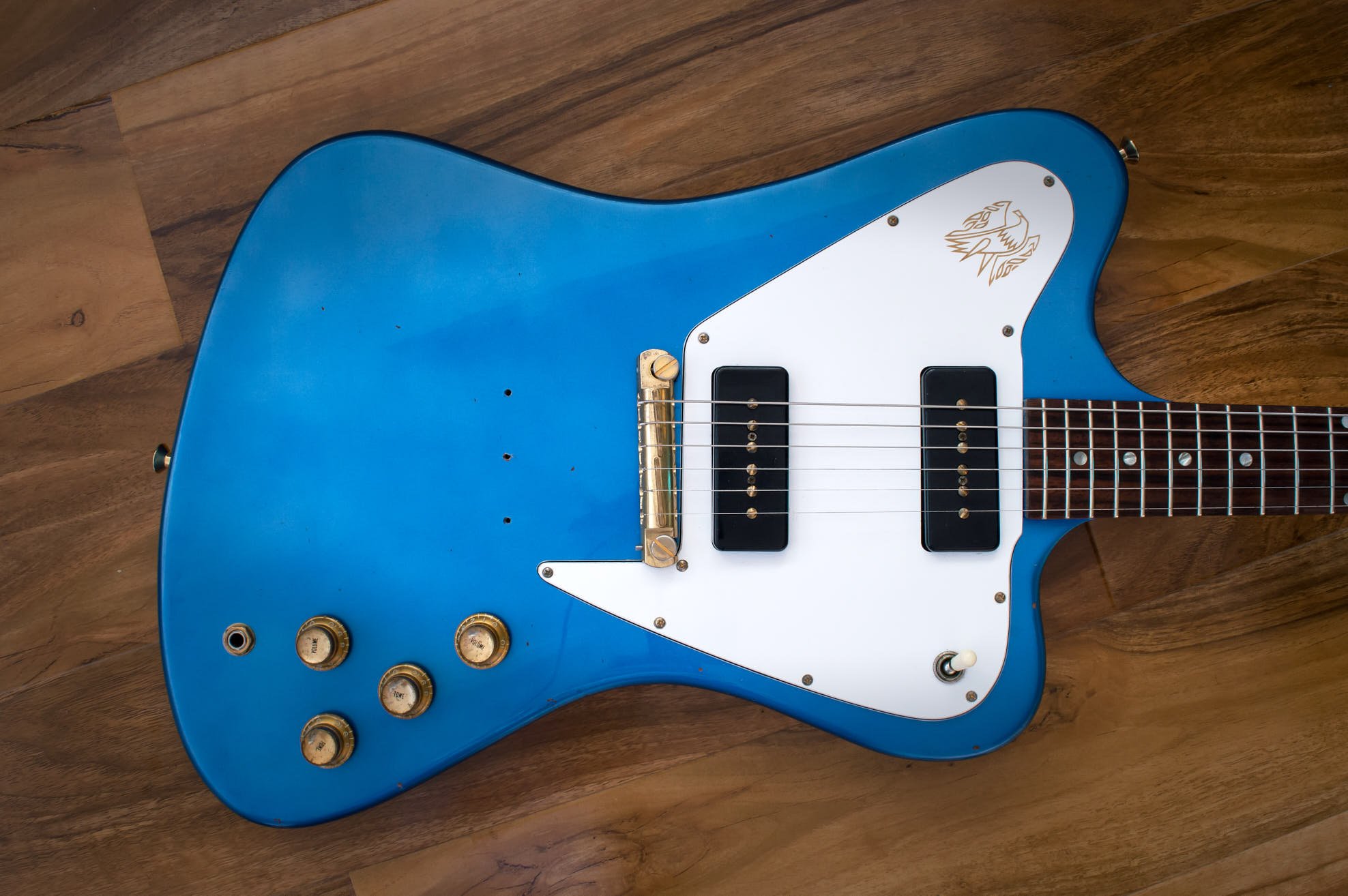
This Firebird tuned out to be incredibly resonant, the neck profile feels wonderful and it sustains for days.
The finished guitar!
Video
The restoration as part of Guitar Magazine’s DIY Workshop series.